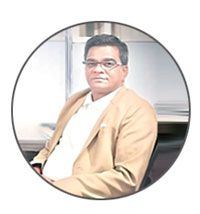
In today’s competitive market, improving productivity and quality is paramount. Cutting tools and strategies play a crucial role in achieving these goals. Every day, the machining industry faces new challenges such as handling exotic materials, complex workpieces, stringent quality parameters, and the need to reduce machining time and cost per component. These challenges drive cutting tool manufacturers to develop advanced tools. Research and development in cutting tools are now highly focused on material and operation-specific solutions, leading to refined substrates, cutting-edge geometries, and next-generation coatings. These innovations result in more controlled chip generation, reduced cutting forces, and lower heat generation.
In this era of intense competition, producing components cost-effectively, quickly, with better quality, and minimal rejection rates is essential. Achieving ideal manufacturing operations involves observing and considering the current process, developing and implementing improvement strategies, and using advanced cutting tool materials. Optimizing manufacturing processes requires transparency and visibility.
The adoption of advanced cutting tool materials like PCBN (Polycrystalline Cubic Boron Nitride) and PCD (Polycrystalline Diamond) directly translates into improved performance metrics. Manufacturers can achieve higher material removal rates (MRR), reduce cycle times, and enhance tool life. For instance, PCBN and PCD tools excel in high-speed machining of hardened steels and aluminum, offering exceptional wear and thermal shock resistance. These advanced materials significantly increase production output and reduce operational costs.
Beyond performance, the evolution of cutting tool materials addresses sustainability concerns. Enhanced durability and efficiency mean fewer tools are needed, reducing material consumption and waste. Additionally, the longevity of these tools minimizes the environmental footprint associated with manufacturing processes, aligning with global sustainability initiatives.
Precision is paramount in modern manufacturing, where tolerances are increasingly tight. Advanced cutting tool materials significantly contribute to achieving and maintaining precise dimensions and surface finishes. This precision enhances product quality and reduces scrap rates, leading to cost savings and improved competitiveness.
PCBN, composed of cubic boron nitride particles sintered together under high pressure and temperature, exhibits exceptional hardness and thermal stability. This makes it ideal for machining hardened steels, cast irons, and superalloys where conventional tools face limitations due to wear and heat resistance issues. On the other hand, PCD, consisting of diamond particles bonded through a sintering process, offers unparalleled hardness and abrasion resistance, making it perfect for machining non-ferrous metals, ceramics, and highly abrasive materials. These tools deliver superior surface finishes, minimizing the need for secondary operations and enhancing product quality. Tighter tolerances and consistent part dimensions contribute to higher-quality outputs, meeting stringent customer requirements effectively.
In conclusion, the adoption of PCBN and PCD tools represents a significant advancement in enhancing productivity across manufacturing sectors. From aerospace to automotive and beyond, these materials enable faster, more precise, and environmentally sustainable machining processes. As technology evolves, so too will the capabilities of cutting tool materials, driving innovation and efficiency across the industrial landscape. Embracing these advancements is not just about staying competitive but also about shaping a future where productivity and sustainability go hand in hand.