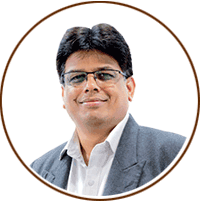
Carl Zeiss continues to set the benchmark in metrology, offering innovative, AI-driven solutions tailored to the evolving needs of diverse industries. From aerospace and medical technology to electronics and electric vehicles, ZEISS combines cutting-edge technologies like 3D X-ray metrology, digital twinning, and AI-enhanced defect detection to deliver unparalleled precision and compliance. By embracing Industry 4.0 principles, ZEISS empowers manufacturers to enhance efficiency, reliability, and innovation across their operations.
Carl Zeiss has always been a pioneer in metrology solutions. Could you share insights into your latest technological advancements?
Carl Zeiss continues to lead the way in metrology with cutting-edge solutions designed for a range of industries, including automotive, aerospace, mechanical engineering, plastics, and medical technology. Our extensive product portfolio includes coordinate measuring machines, optical and multi-sensor systems, as well as advanced metrology software. Among the most notable innovations are 3D X-ray metrology for quality inspection and industrial microscopy for material analysis, enabling unparalleled precision and efficiency in quality assurance processes. These technologies empower businesses to achieve higher accuracy and reliability, addressing even the most complex inspection requirements.
With the rise of Industry 4.0, how is ZEISS integrating AI into its metrology solutions?
Industry 4.0 has ushered in an era of intelligent manufacturing, and ZEISS is at the forefront of this transformation. A key example of this integration is Zeiss Volume Inspect, utilized in X-ray and computed tomography (CT) equipment. Manufacturing processes often result in hidden defects that can compromise component functionality. ZEISS’s Automated Defect Detection (ZADD) software leverages artificial intelligence to identify and evaluate such defects early.
The ZADD Segmentation app, powered by machine learning, specializes in detecting even small and fuzzy defects in components, ensuring precision even when image quality is suboptimal. By integrating AI with CT data inspection, ZADD supports component development, process optimization, and fault analysis, making it an indispensable tool for modern manufacturing challenges.
Aerospace and space manufacturing demand precision, safety, and stringent processes. How do ZEISS metrology solutions ensure compliance with these standards?
Aerospace and space manufacturing require uncompromising precision and adherence to rigorous quality standards. ZEISS metrology solutions streamline aircraft development, quality assurance, and maintenance checks through technologies such as material analysis, automation, X-ray, and CT scanning.
For space components, such as satellites and spacecraft, ZEISS’s ATOS products play a pivotal role. These solutions facilitate the creation of precise digital twins, enabling low-volume production runs and adaptable processes for future scalability. The incorporation of digital twinning, alongside precise 3D inspection, ensures that additive manufacturing for complex parts meets the highest quality standards. This approach provides manufacturers with the flexibility to adapt quickly while maintaining stringent compliance.
How does ZEISS address the high level of precision and reliability required in medical device manufacturing and compliance with regulatory bodies?
The medical technology industry operates under stringent regulatory frameworks to prioritize patient safety. Global companies must navigate varying regulations, including the European MDR (Medical Device Regulation), the FDA’s guidelines in the U.S., and ISO 13485, which specifically addresses medical device manufacturing.
ZEISS’s metrology solutions are designed to meet these stringent requirements. Our microscopy solutions ensure compliance with DIN EN ISO 13485 and FDA 21 CFR Part 11, facilitating precision in manufacturing orthopaedic implants, medical plastics, and R&D processes. Moreover, our connected quality intelligence portfolio offers tailored hardware and software solutions that ensure compliance while driving productivity and precision.
With the growing demand for compact and efficient electronics, how does ZEISS ensure precision in PCB inspection and component testing?
ZEISS offers comprehensive solutions for the electronics industry, covering areas such as consumer electronics, automotive electronics, and telecom electronics. These solutions span the entire process, from product development to design verification testing, to mass production quality inspection. Key areas include dimensional measurement, assembly inspection, non-destructive analysis of modules, defect analysis, and failure analysis.
For example, structural parts in electronics, such as smartphone housings, require high-speed and flexible design verification. ZEISS’s CT systems and 3D X-ray technologies enable fast, non-destructive scanning, supporting defect analysis and dimensional measurement in a single scan. This capability ensures faster time-to-market while maintaining high standards of quality and precision.
What specific metrology solutions does ZEISS provide for inspecting and ensuring the reliability of EV components?
With over 1,000 global customers in the electric vehicle (EV) sector, ZEISS is a trusted partner in this rapidly growing industry. Our solutions span the entire lifecycle of EV components, from research and development to production. We segment EV components into four key areas: batteries, e-motors, power electronics, and transmissions.
For instance, in e-motor manufacturing, challenges include achieving high RPM and torque while maintaining a compact and lightweight design. ZEISS’s metrology solutions address these challenges by enabling precise inspection of hairpins, sheet stacks, weld seams, rotors, and shafts.
Rotors, in particular, demand tight shape and location tolerances due to the high performance and speed requirements of e-motors. ZEISS CMMs with active scanning technology are ideal for inspecting these components. Long stylus extensions allow measurements to be taken far from the rotor’s magnetic field, ensuring stable and accurate results. These solutions not only enhance safety and reliability but also drive efficiency in EV component manufacturing.
Carl Zeiss remains a trailblazer in metrology, addressing the diverse needs of industries with innovative, AI-driven solutions. From aerospace and medical technology to electronics and electric vehicles, ZEISS’s commitment to precision, compliance, and technological advancement ensures that manufacturers can meet the highest standards of quality and performance. By integrating advanced metrology with Industry 4.0 principles, ZEISS continues to empower industries to achieve greater efficiency, reliability, and innovation.
Visit : www.zeiss.co.in