Probably very few, Edward Deming’s 94-6 Rule states that 94% of problems within an organization are caused by (or lack of) a SYSTEM, while only 6% can be attributed to PEOPLE. This rule suggests that CEOs must focus on improving the system rather than solely focusing on its machines and people. Most CEOs have been taught that good leadership is about managing men. They believe that managing the 6% of shop floor staff alone will improve performance and enhance shop floor productivity. Even the best operators have little chance of overcoming poor workplace systems. In fact, a bad system will beat a good operator every time.
Industry 4.0 and the 96-4 RuleÂ
Deming’s belief that improving systems yields better results is demonstrated by Industry 4.0. Shop floors that adopt Industry 4.0 automate their production data collection systems, leading to better-informed, data-driven decisions, resulting in increased productivity and higher profits. Leanworx Industry 4.0 helps you put the Deming’s 96-4 rule into practice.
Leanworx is an AI-powered Cloud based system designed to help managers monitor and optimize production by providing precise, real-time data on various manufacturing parameters such as machine performance, output, operator performance, and productivity. By continuously tracking these metrics, Leanworx helps managers pinpoint issues, such as unexpected downtime or inefficiencies, the moment they arise. With this instant visibility into production processes, managers can make quick, informed decisions to address problems before they escalate. By minimizing downtime and ensuring that machines and personnel are operating at peak efficiency, Leanworx helps drive better resource utilization, reduce costs, and ultimately, achieve higher profitability.
What Shop Floor Problems Does Leanworx Solve?Â
Traditionally, collecting shop floor data is a person-dependent system. Managers currently obtain data via a paper-and-people-based data chain. Data accuracy depends on people’s memory and honesty, and managers receive this inaccurate data after 24 to 36 hours. Wrong data leads to wrong decisions, and late data leads to no decisions.
Leanworx transforms this archaic person-dependent system into a person-independent system. Leanworx captures data from the machines directly and reports to the managers via an AI-powered cloud application. The benefits offered by Leanworx are immense: Decision-makers receive instant and accurate data, better diagnoses, and fast responses to problems, resulting in higher machine utilization and increased profits.
Leanworx displays production and downtimes on real-time dashboards and Andon boards. It generates reports and historical trends on production quantity, productivity (OEE, downtimes), quality, maintenance, consumable usage, energy usage, operator efficiency, etc. For urgent issues like machine breakdowns, it sends alerts via mobile phone and email. It can also send data to external software applications like ERP.
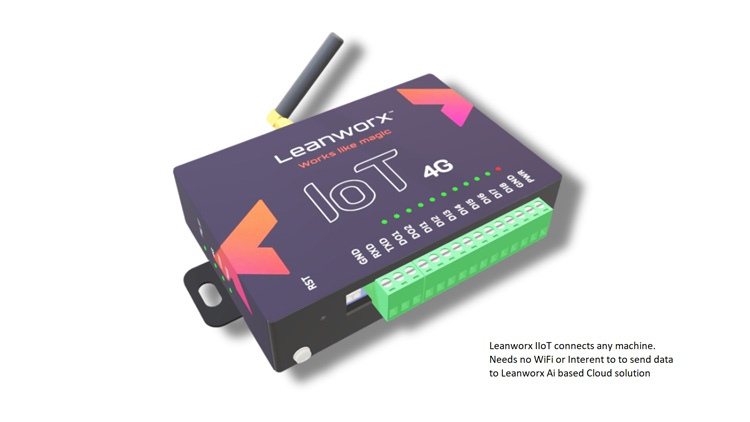
What Makes Leanworx Unique?Â
The core product design philosophy centers on five non-negotiable principles, captured by the acronym T.R.U.M.P: Tamper-proof, Reliable, Universal Machine Interface, Maintenance-free, and Plug-and-Play.
Most MSMEs have limited or no IT infrastructure on their shop floor. They hesitate to spend on expensive cabling, other IT hardware, and the costs of employing an IT resource to maintain a complex Industry 4.0 system. The beauty of Leanworx IIoT is that it connects the machine directly to the cloud and therefore does NOT need any IT infrastructure to function—no internet, no LAN cabling, no server, no database to maintain, and finally, no dedicated IT person to maintain the system. That’s not all; IIoT takes a mere 30 minutes to connect to each machine.
Is Leanworx affordable?Â
Surprisingly, Leanworx costs less than a cup of coffee per day, per machine, making it very affordable even for SMEs. Since no one size fits all, Leanworx comes in five scalable software modules; it is always advisable to start small and upgrade as their needs grow.
Real-Life Success Stories
Some of the most profitable shop floors run on Leanworx. Many auto parts manufacturers, aerospace and defence parts makers, OEMs of hydraulic equipment, gear manufacturers in foundries, forging, and machining companies are seeing immense productivity gains. Five key benefits reported by users include:
- Machine utilization improved by 28%
- Deferred CapEx on machines for 2 years
- Drastically improved operator work ethics
- Incentivized high performance operators
- Significantly reduced MTTA breakdowns