The secure and stable clamping of workpieces is critical to achieving precision in machining. Traditional clamping methods, such as vices and clamps, often fall short, especially when dealing with thin-walled components, leading to distortion and vibrations that impair machining accuracy and surface finish. To address these challenges, Schmalz, a leader in vacuum automation, has introduced the Matrix-Plate MPL, a modular vacuum clamping system designed for CNC machining applications in metal and plastic industries
Innovative Vacuum Clamping for Enhanced Precision
The Matrix-Plate MPL departs from traditional clamping techniques by employing advanced vacuum technology to secure workpieces with precision. Central to this system is the matrix plate, a perforated aluminum base equipped with an integrated vacuum distribution grid. This grid ensures consistent and homogeneous vacuum pressure across the entire plate, generating a strong and uniform holding force. The MPL system offers various grid sizes, allowing users to accommodate different workpiece dimensions and control vacuum levels as needed.
One of the key strengths of the MPL system is its modularity. In addition to the matrix plate, the system includes interchangeable clamping elements that provide exceptional flexibility in CNC machining. The MPL can be easily integrated into existing machining setups, whether mounted directly onto a CNC machine table with clamping claws, a vice, or a zero-point clamping system, ensuring minimal machine downtime.
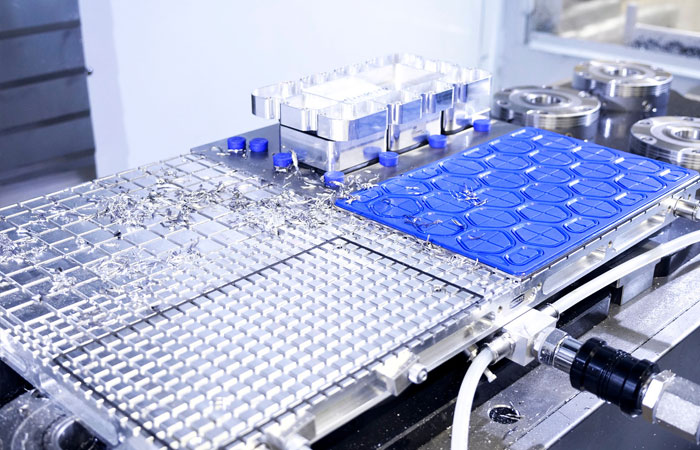
Advanced Clamping Solutions
The MPL system includes several innovative components that enhance its versatility:
Steel-Plate ISST: This adapter plate enables the use of Schmalz vacuum blocks, allowing for adjustable suction points, which are crucial for clamping workpieces with complex geometries. This ensures stability during intricate machining processes.
FlexMat SFM: An elastomeric mat that provides a flexible clamping surface, ideal for parts with complex shapes or cutouts. The elastomer deforms to match the workpiece’s shape, ensuring effective sealing even with uneven surfaces.
Technical Advantages and Industry Applications
The MPL system offers several advantages that translate into enhanced machining processes:
Reduced Distortion and Vibration: By avoiding mechanical clamps, the MPL system minimizes distortion, particularly in thin-walled components, resulting in higher machining accuracy and superior surface finishes.
Material Compatibility: The MPL system can securely clamp both ferrous and non-ferrous metals, as well as non-metallic materials like plastics, expanding its application across various industries.
Efficiency Gains: The pre-assembled matrix plate and modular clamping elements reduce setup times, leading to increased efficiency on the shop floor.
Enhanced Safety and Productivity: The system can be equipped with first-class accessories, such as vacuum supply and monitoring tools, to enhance operator safety and allow for higher machining speeds.
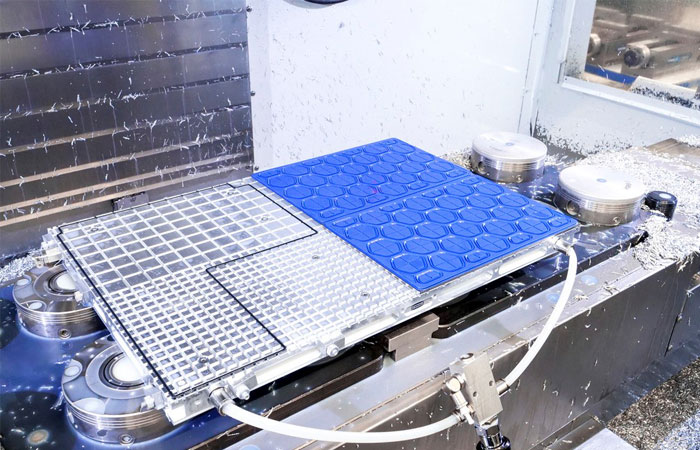
Conclusion: A New Era in Machining Precision
The Schmalz Modular Clamping System MPL represents a significant advancement in CNC machining. Its use of vacuum technology and modular design reduces deformation and vibration, improving machining quality and efficiency. Moreover, its adaptability to different geometries and workpiece dimensions offers unmatched flexibility on the shop floor, making it a valuable tool for industries requiring precision machining, such as aerospace, automotive, and electronics.
Contact for Inquiries Schmalz India Private Limited : marketing@schmalz.co.in